Work Breakdown Structure (WBS) elements are normally used to define the construction planning, organization, and control of a project.
In SAP Plant Maintenance (SAP PM), you can also use WBS elements to carry out pure budget planning and control; in this post, we’ll look at them here from that perspective.
Creating WBS Elements in SAP PM
To use WBS elements, use Transaction CJ01 to define a project (for example, plant maintenance budgeting) and then use Transaction CJ11 to create several levels of WBS elements as a basis for a budgetary structure. The following are possible criteria you can use for orientation:
- Asset-oriented: For example, each top-level functional location has a budget.
- Maintenance group-related: For example, mechanical workshop, electrical workshop.
- Activity-related: For example, for maintenance, repairs, overhaul.
Budget planning is then normally done in a top-down manner and assigned to the WBS elements of each budget on an annual basis using Transaction CJ30 (see the figure below).
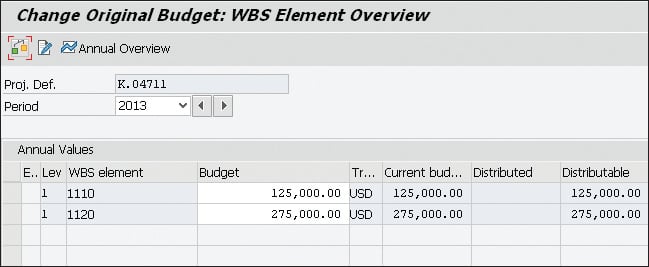
If you want to distribute budgets on a system basis, you should then enter the WBS element responsible for the budget into the master record of the technical object, as shown in the figure below.
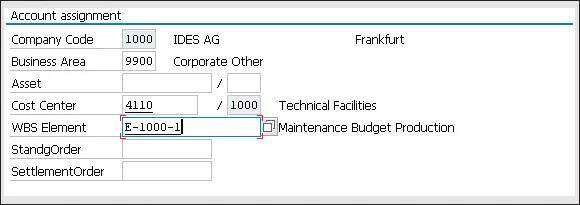
Once you have completed this and set up Customizing accordingly, the WBS element is automatically transferred to the order, and thus, the order is assigned to the WBS element. The assignment can be seen in the order on the Additional data tab (see the figure below), where you can also perform a manual assignment or change an existing one.
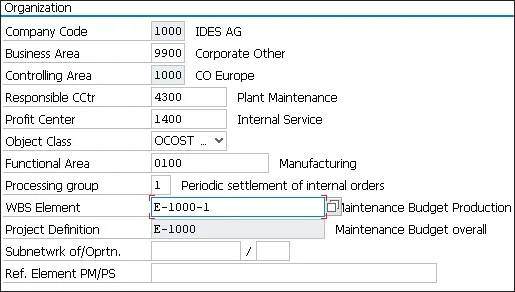
Assigning WBS Elements in SAP PM
Assigning orders to WBS elements automatically can be customized by using user exit IWO10010 with a custom assignment routine. Depending on the technical object, for example, you can find the right WBS element here for the order type and maintenance activity type. This automatic assignment saves the user time-consuming manual assignment, increasing acceptance.
The budget availability control of WBS elements involves both an active and a passive availability control:
- Active availability control: Active availability control means that, for each actual posting (for example, time confirmation, goods issue), the system checks whether the WBS budget is sufficient. Depending on the settings in the budget profile, a warning or error message may be issued.
- Passive availability control: Passive availability control means that the system provides you with sufficient reporting options to check your budgets. Costs charged to the order then appear in the budget overview for each WBS element.
The following figure (Transaction S_ALR_87013557) shows a WBS with three elements to which budgets were assigned. Ongoing plant maintenance tasks are then shown in the actual costs and/or the remaining availabilities.
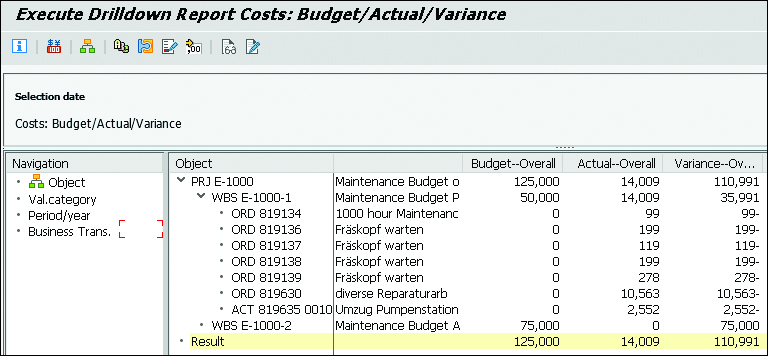
Budgeting with WBS Elements in SAP PM
Behind the WBS elements, either an actual plant maintenance project exists, or you can use the elements for purely budgeting purposes in order to manage the ongoing budget. Thus, from a plant maintenance perspective, you can budget all plant maintenance activity using WBS elements.
To budget with WBS elements, the following prerequisites must be satisfied:
- You have assigned your technical objects (equipment, functional locations) a WBS element in the master record.
- You have used the Customizing function Define Transfer of Project or Investment Program for each order type with an assignment with an “X” to ensure that the WBS elements will be transferred from the master record into the order.
- You have used the Customizing function Maintain Budget Profile to create a budget profile and assign your WBS elements.
You have used the Customizing function Define Tolerance Limits to define the limits for your controlling area and your budget profile at which warning messages and error messages will be generated, thus activating the active availability control.
Conclusion
WBS elements can be an attractive tool for budget monitoring because you’ll have active availability control, the activation of which prevents the order budget from being exceeded due to actual postings. With reporting tools, you also have the option of passive availability control.
Editor’s note: This post has been adapted from a section of the book Plant Maintenance with SAP: Business User Guide by Karl Liebstückel.
Comments