When it comes to your materials planning, it pays to have some extra raw materials laying around, an idea known as safety stock. In SAP, safety stock can be calculated and tracked in SAP Production Planning (PP).
Types of Safety Stock in SAP
The SAP ERP system offers two types of safety stocks: absolute safety stock and safety days’ supply. The absolute safety stock enables the system to subtract it from material availability calculations (net requirements calculations). The safety stock must always be available to cover for unforeseen material shortages or unexpected high demand.
For days’ supply/safety time, the system plans the goods receipt in advance by the period specified as safety time. Thus, planned days’ supply of the stock, in fact, corresponds to the number of days specified as safety time. The system shifts backs the date of the receipts by the number of working days and also takes the factory calendar into account.
You make the relevant entries in the MRP 2 view of the material master. The system refers to the planning of a safety days’ supply as safety time. To consider the safety time, you need to set the Safety time ind. to “1” (for independent requirements) or “2” (for all requirements), and then also give the Safety time/act.cov. in days. Further, you can define deviations from the constant safety time using a safety time period profile (STime period profile field).
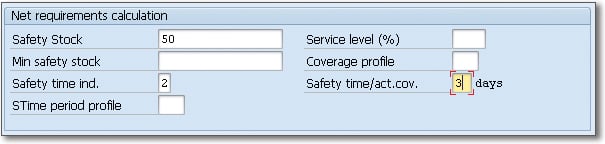
Let’s take a look at how the safety stock availability can be used in net requirements calculations and also the selection method that the system uses for receipts.
Safety Stock Availability
To avoid the unnecessary creation of planned orders for a smaller quantity, which can otherwise be covered by the safety stock, you can define the percentage (share) of safety stock that the system can use in such business scenarios.
For example, during the MRP run, the system assesses a shortage of 2 PC of a material. You have, however, maintained a safety stock of 40 PC for this material, which the system doesn’t consider in the MRP run.
If you define that a 10% safety stock can be used to account for smaller shortages, which for this example means that 4 PC come from safety stock, then the system can cater to this small requirement or shortage of 2 PC from the 4 PC available from safety stock and no longer creates a procurement proposal.
To define the safety stock parameters, use configuration (Transaction SPRO) menu path, Logistics > Production > Material Requirements Planning > Planning > MRP Calculation > Stocks > Define Safety Stock Availability. For this example, the system can consider 10% of the safety stock for Plnt 3000 and MRP group 0010 for net requirements calculation (see below). You eventually assign the MRP group in the MRP 1 view of the material master.
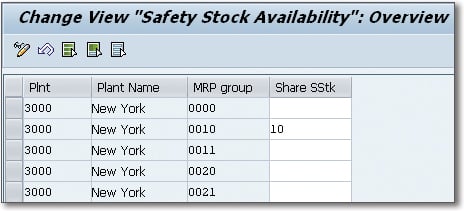
Master Data Selection
For material that’s produced in-house, you also create a bill of materials (BOM) and routing or master recipe. There might be several alternatives available for a BOM or a routing, so you can control the selection of alternatives. This ensures that the system is able to assign the relevant BOM and routing to the created planned orders, and it enables you to perform functions such as availability checks, and so on.
With the right control in place, the system automatically assigns the correct selection or alternate in the planned orders created from the planning run. This is accessed and managed in the MRP 4 view of the material master (Transaction MM02) as shown below.
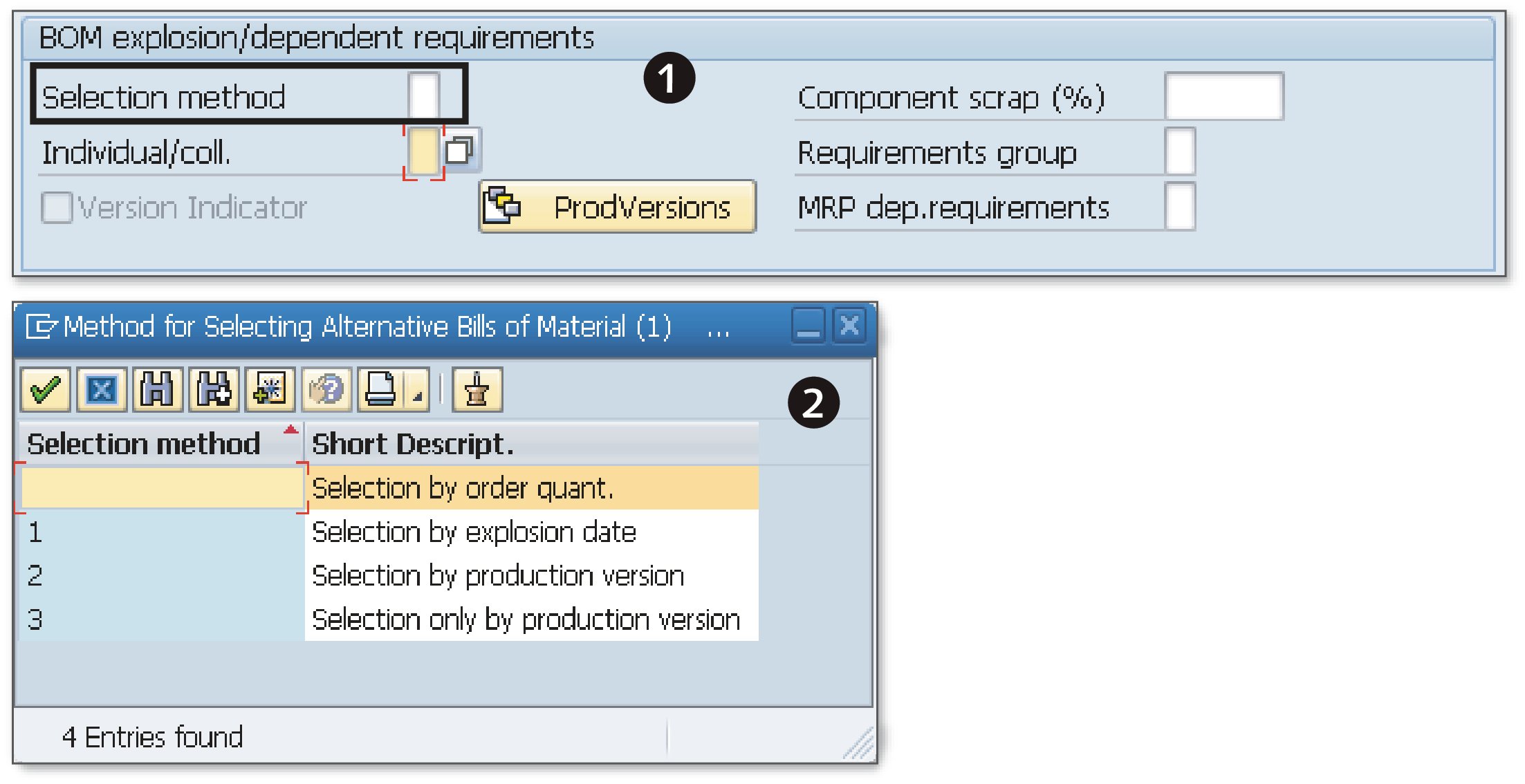
Conclusion
Planning for issues with safety stock in SAP is an important step for any production planner to undertake. In this blog post, we took a look at the types of safety stock SAP PP allows, how to make it available, and how to select master data for in-house material.
Editor’s note: This post has been adapted from a section of the book Production Planning and Control with SAP ERP by Jawad Akhtar. Jawad is an SAP logistics and supply chain management expert with a focus on business sales and delivery. He earned his chemical engineering degree from the Missouri University of Science and Technology in the United States. He has more than 20 years of professional experience, 16 of which have been spent working with SAP systems. He has experience working on several large-scale, end-to-end SAP implementation project lifecycles, including rollouts. He works with SAP clients to help them identify the root causes of business issues and address those issues with the appropriate SAP products and change management strategies. He now focuses on next-generation SAP products such as SAP S/4HANA, SAP Integrated Business Planning, SAP Ariba, and SAP Customer Experience.
This post was originally published 3/2020.
Comments